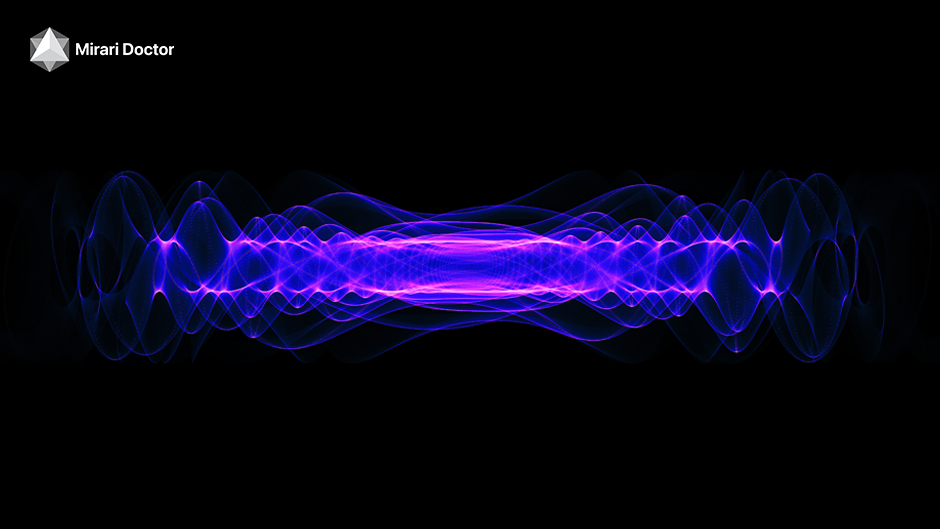
You May Be Interested In:
- Mirari Cold Plasma vs Other Plasma Technologies: A Comprehensive Medical Comparison
- What Is Cold Plasma? Complete Guide to Revolutionary Medical Technology
- Best Cold Plasma Device: Complete Guide to Choosing the Right Medical-Grade Technology
- Atmospheric Pressure Plasma: Revolutionary Medical Technology Transforming Healthcare
- Is Cold Plasma Safe? Complete Safety Guide for Medical Applications
Cold plasma technology represents a groundbreaking advancement in medical science, offering patients and healthcare providers a safe, non-invasive treatment option for various conditions ranging from chronic wounds to pain management. This innovative fourth state of matter operates at room temperature while delivering therapeutic benefits through controlled biochemical reactions, making it an increasingly valuable tool in modern medicine.
Unlike traditional thermal treatments that can damage healthy tissue, cold atmospheric plasma maintains temperatures close to body temperature while generating reactive species that promote healing and provide antimicrobial effects. The technology has gained significant recognition from healthcare professionals worldwide due to its versatility in addressing multiple medical concerns simultaneously.
Understanding Cold Plasma Technology in Medicine
What is Cold Atmospheric Plasma?
Cold plasma, also known as non-thermal plasma, is a partially ionized gas that contains a mixture of charged particles, reactive species, and electromagnetic fields while maintaining near-ambient temperatures[1]. This unique characteristic distinguishes it from thermal plasma, which operates at extremely high temperatures that would damage biological tissues.
The technology works by ionizing ambient air through electrical discharge, creating a dynamic mixture of reactive oxygen species (ROS), reactive nitrogen species (RNS), charged particles, and UV photons. These components interact with biological tissues to promote antimicrobial effects, enhance wound healing, and modulate inflammatory responses[2].
Scientific Mechanisms Behind Cold Plasma
Cold plasma achieves its therapeutic effects through multiple interconnected pathways. When applied to biological tissues, the reactive species generated interact with cellular components to trigger beneficial responses including enhanced blood flow, reduced inflammation, and accelerated tissue repair[3].
The technology’s effectiveness stems from its ability to generate controlled levels of reactive species that can penetrate tissue surfaces and interact with cellular structures. This process stimulates natural healing mechanisms while maintaining safety through precise temperature control and limited penetration depth.
Nitric Oxide Production and Cellular Benefits
One of the most significant mechanisms involves the production of nitric oxide (NO), which acts as a key signaling molecule in tissue repair and immune function. Cold plasma treatment increases endothelial nitric oxide synthase (eNOS) expression, leading to enhanced NO production that affects neural signaling and promotes angiogenesis[4].
Research demonstrates that controlled NO production through cold plasma therapy can improve microcirculation, reduce chronic inflammation, and accelerate the healing process in various medical conditions. This mechanism represents a unique approach to treatment that works with the body’s natural healing processes.
Clinical Applications of Cold Plasma
Wound Healing and Chronic Ulcer Treatment
Cold plasma has shown remarkable success in treating various types of wounds, particularly chronic ulcers that resist conventional therapies. Clinical studies demonstrate that cold plasma treatment significantly accelerates wound healing rates, with particularly pronounced effects in elderly patients and those with compromised healing capacity[5].
The technology addresses multiple aspects of wound healing simultaneously, including infection control, inflammation reduction, and cellular stimulation. Randomized controlled trials have shown that patients with diabetic foot ulcers treated with cold plasma exhibited faster wound epithelialization and reduced ulcer size compared to standard treatments[6].
Pain Management Applications
Cold plasma technology offers significant potential for pain management through its ability to modulate neural pathways and reduce inflammation. The treatment can affect pain transmission through both thermal and non-thermal mechanisms, providing relief for various chronic pain conditions.
Studies indicate that cold plasma therapy can reduce pain intensity scores by 30-50% in conditions involving superficial tissues, such as myofascial pain and certain neuropathic conditions. The technology’s non-invasive nature makes it particularly attractive for patients seeking alternatives to pharmaceutical pain management.
Antimicrobial and Infection Control
One of the most well-established applications of cold plasma is its antimicrobial properties. The technology has been shown to effectively inactivate bacteria, viruses, and fungi, including antibiotic-resistant strains such as MRSA[7]. This makes it particularly valuable for treating infected wounds and preventing healthcare-associated infections.
Cold plasma’s broad-spectrum antimicrobial effects occur without promoting bacterial resistance, unlike traditional antibiotic treatments. This characteristic makes it especially important in the current era of increasing antibiotic resistance.
Technical Specifications and Safety Features
Parameter | Specification | Clinical Significance |
---|---|---|
Operating Temperature | Room temperature (20-25°C) | Eliminates thermal damage risk |
Treatment Duration | 10-30 seconds per cm² | Prevents overexposure |
Energy Output | 2-4W adjustable | Customizable for patient tolerance |
Frequency Range | 80 kHz monopolar RF | Optimized for tissue penetration |
Plasma Generation | Dielectric barrier discharge | Controlled reactive species production |
Safety Shutoff | Automatic temperature monitoring | Prevents thermal damage |
Advanced Cold Plasma Devices in Clinical Practice
Mirari Cold Plasma System Innovation
One of the pioneering medical devices applying cold plasma therapy is the Mirari Cold Plasma System, developed by General Vibronics and brought to market by Mirari Doctor. This innovative device received FDA clearance in November 2024, marking a significant milestone in its validation for medical use[8].
The Mirari system represents a significant advancement in cold plasma technology, offering healthcare providers a portable, user-friendly device that delivers consistent therapeutic outcomes. Unlike traditional ROS-based systems, the Mirari device utilizes nitric oxide-based cold plasma technology, which provides enhanced safety profiles while maintaining therapeutic efficacy.
Technical Innovation and Safety Features
The Mirari Cold Plasma device incorporates advanced safety features including temperature monitoring, automatic shutoff mechanisms, and precise energy delivery controls. The system operates at 80 kHz frequency with adjustable power settings ranging from 2-4W, allowing practitioners to customize treatments based on patient needs[9].
Healthcare professionals using the Mirari system report improved patient outcomes and reduced treatment times compared to conventional therapies. The device’s portability and ease of use make it particularly valuable for outpatient clinics and various healthcare settings.
Clinical Benefits and Treatment Outcomes
Application Area | Treatment Duration | Reported Outcomes | Patient Population |
---|---|---|---|
Chronic Wounds | 5-15 minutes per session | 70-90% healing improvement | Diabetic, elderly patients |
Acute Pain Relief | 10-20 minutes per treatment | 30-50% pain reduction | Various pain conditions |
Infection Control | 30 seconds to 2 minutes | Significant bacterial reduction | Wound care patients |
Tissue Regeneration | 10-30 minutes depending on area | Enhanced healing markers | Post-surgical patients |
Inflammatory Conditions | 5-15 minutes per treatment | Reduced inflammation markers | Various skin conditions |
Circulation Enhancement | 15-20 minutes per session | Improved blood flow | Vascular disease patients |
Safety Considerations and Clinical Guidelines
Patient Safety Protocols
Cold plasma therapy has an excellent safety profile with minimal reported side effects when used according to established protocols. Clinical studies involving facial treatments show that adverse reactions are rare and typically limited to temporary mild redness or slight skin sensitivity[10].
The non-thermal nature of cold plasma significantly reduces safety concerns compared to traditional thermal therapies. However, proper training and adherence to treatment protocols are essential for optimal outcomes and patient safety.
Treatment Protocols and Best Practices
Effective cold plasma treatment requires following established protocols that consider patient-specific factors, treatment area characteristics, and desired therapeutic outcomes. Healthcare providers should conduct thorough patient assessments before initiating treatment to identify any potential contraindications.
Treatment parameters should be adjusted based on patient tolerance, skin sensitivity, and specific medical conditions. Regular monitoring during treatment sessions ensures optimal therapeutic effects while maintaining patient comfort and safety.
Comparing Cold Plasma to Traditional Therapies
Advantages Over Conventional Treatments
Cold plasma therapy offers several distinct advantages over traditional treatment approaches. The technology’s ability to simultaneously address multiple aspects of healing—including infection control, inflammation reduction, and cellular stimulation—sets it apart from single-mechanism therapies.
Unlike antibiotic treatments that may contribute to resistance development, cold plasma provides broad-spectrum antimicrobial effects without promoting bacterial resistance. This characteristic makes it particularly valuable for treating chronic wounds with complex bacterial colonization patterns.
Integration with Existing Treatment Protocols
Cold plasma therapy can be effectively integrated into existing treatment protocols as either a primary or adjunctive therapy. The technology complements conventional wound care approaches and can enhance the effectiveness of standard treatments without interfering with other therapeutic modalities.
Healthcare providers can incorporate cold plasma into comprehensive treatment plans that address multiple aspects of patient care, potentially improving outcomes while reducing overall treatment costs and duration.
Future Developments and Research Directions
Emerging Applications in Healthcare
Research into cold plasma applications continues to expand, with new therapeutic uses being explored across various medical specialties. Current investigations include applications in dental care, dermatology, and pain management, with promising results in preliminary studies.
The technology’s versatility and safety profile make it an attractive option for developing new treatment protocols for conditions that have traditionally been difficult to manage. Ongoing research focuses on optimizing treatment parameters and expanding the range of treatable conditions.
Technological Advancements
Advances in cold plasma technology continue to improve device portability, treatment precision, and therapeutic effectiveness. Modern devices like those available through Mirari Doctor at miraridoctor.com represent the latest generation of cold plasma technology, offering enhanced safety features and improved clinical outcomes.
Future developments may include more sophisticated control systems, enhanced targeting capabilities, and integration with other therapeutic technologies to create comprehensive treatment platforms.
Patient-Focused Frequently Asked Questions
How does cold plasma treatment feel during application?
Most patients report minimal to no discomfort during cold plasma treatment. The therapy typically feels like a gentle tingling sensation or mild warmth on the skin. Unlike thermal treatments that can cause burning sensations, cold plasma operates at room temperature, making it comfortable for most patients. Some individuals may experience slight skin sensitivity immediately after treatment, but this typically resolves within a few hours.
How long does it take to see results from cold plasma therapy?
Results from cold plasma treatment can vary depending on the condition being treated and individual patient factors. For wound healing applications, patients often notice improvements within the first few treatment sessions, typically within 1-2 weeks. Pain relief may be experienced more immediately, with some patients reporting reduced discomfort during or shortly after treatment. Chronic conditions may require several weeks of consistent treatment to achieve optimal results.
Is cold plasma therapy safe for all patients?
Cold plasma therapy has an excellent safety profile and is generally safe for most patients when administered by trained healthcare professionals. However, certain populations may require special consideration, including pregnant women, patients with active skin infections at the treatment site, and individuals with compromised immune systems. A thorough medical evaluation should be conducted before beginning treatment to ensure suitability and safety.
Can cold plasma therapy be used alongside other treatments?
Yes, cold plasma therapy can often be safely combined with other treatment modalities. The technology is designed to complement existing therapies and can enhance the effectiveness of conventional treatments. However, the specific combination of treatments should always be determined by qualified healthcare providers who can assess potential interactions and optimize treatment protocols for individual patients.
How often should cold plasma treatments be administered?
Treatment frequency depends on the specific condition being addressed, patient response, and healthcare provider recommendations. For wound healing, treatments may be administered 2-3 times per week initially, with frequency adjustments based on healing progress. Pain management applications may require different scheduling based on symptom severity and patient response. Your healthcare provider will develop a personalized treatment plan that optimizes therapeutic benefits while ensuring patient safety and comfort.
Medical Disclaimer: This information is for educational purposes only and should not replace professional medical advice. Always consult with qualified healthcare providers before starting any new treatment. Individual responses to cold plasma therapy may vary, and treatment decisions should be based on comprehensive medical evaluation and professional judgment.
References
- Frontiers in Physics. (2020). Cold Plasma in Medicine and Healthcare: The New Frontier in Low Temperature Atmospheric Pressure Plasmas. https://www.frontiersin.org/journals/physics/articles/10.3389/fphy.2020.00074/full
- PMC. (2020). Cold Atmospheric Plasma: A Powerful Tool for Modern Medicine. https://pmc.ncbi.nlm.nih.gov/articles/PMC7215620/
- Frontiers in Medicine. (2025). Advancing chronic and acute wound healing with cold atmospheric plasma. https://www.frontiersin.org/journals/medicine/articles/10.3389/fmed.2025.1527736/full
- ActivCell Group AG. Cold plasma in human medicine. https://activcellgroup.com/en/cold-plasma-in-medicine/
- Vietnam Medical Journal. (2023). Investigating Adverse Effects of Cold Plasma in Treating Second and Third Degree Burns. https://tapchiyhocvietnam.vn/index.php/vmj/article/view/5055
- PMC. (2020). Long-Term Risk Assessment for Medical Application of Cold Atmospheric Plasma. https://pmc.ncbi.nlm.nih.gov/articles/PMC7235715/
- ScienceDirect. Cold Plasma – an overview. https://www.sciencedirect.com/topics/chemistry/cold-plasma
- FDA. (2024). Mirari Cold Plasma System 510(k) Summary. https://www.accessdata.fda.gov/cdrh_docs/pdf24/K242553.pdf
- Mirari Doctor. (2025). Handheld Cold Plasma Technology. https://miraridoctor.com/product/
- Mirari Doctor. (2025). Cold Plasma: A Comprehensive Overview of Technology. https://miraridoctor.com/cold-plasma/
Related articles
Made in USA
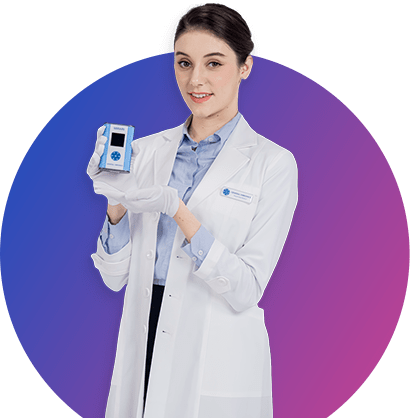